A variety of processes are being used for removing CO2 from natural gas in petrochemical industries. Several basic mechanisms are involved to achieve selective
separation of gas constituents. These may include physical or chemical absorption,
adsorption on a solid surface, membrane separation, cryogenic separation and chemical
conversion.
Carbon dioxide is a noncombustible constituent of biogas lowers its heat value. Removal of carbon dioxide is not necessary when gas is to be used for cooking or lighting purposes only. A number of methods have been developed for CO2 removal (scrubbing) which depending upon the technique involved are called water-scrubbing, caustic-scrubbing, solid absorption, liquid absorption and pressure separation.
A brief description of these methods is as follows:
For biogas scrubbing physical/chemical absorption method is generally applied as they
are effective even at low flow rates that the biogas plants are normally operating at. Also, the method is less complicated, requires fewer infrastructures and is cost-effective.
Method # 1. Water Scrubbing:
One of the easiest and cheapest methods involves the use of pressurized water as an absorbent. The raw biogas is compressed and fed into a packed bed column from the bottom; pressurized water is sprayed from the top. The absorption process is, thus a counter-current one. This dissolves CO2 as well as H2S in water, which are collected at the bottom of the tower.
In this method, gas is made to pass through water which absorbs part of CO2. The inherent limitation of this method is that it requires a large quantity of water. Based on studies carried out by H.M. Lapp, 7 ft3 (0.2 m3) of biogas at 68°F (20°C) and 1 atmospheric pressure (1.03 kg/cm2) requires 2.7 gallons (12.3 litres) of water for CO2 removal. CO2 is highly soluble in water. Spent water following absorption of CO2 becomes acidic and hence unsuitable for several applications as it corrodes metallic surface it comes in contact with.
Method # 2.CHEMICAL ABSORPTION
Caustic Scrubbing:
Chemical absorption involves
the formation of reversible chemical bonds between the solute and the solvent.
Regeneration of the solvent, therefore, involves breaking of these bonds and
correspondingly, a relatively high energy input. Chemical solvents generally
employ either aqueous solutions of amines, i.e. mono-, di- or tri-ethanolamine
or an aqueous solution of alkaline salts, i.e. sodium, potassium and calcium
hydroxides. Biswas et al. reported that by bubbling biogas through 10% an aqueous solution of mono-ethanolamine (mea), the co2 content of the biogas was
reduced from 40 to 0.5-1.0% by volume. A solution can be completely regenerated
by boiling for 5 min and thus can be used again
This method works on the principle that when caustic solutions are made to react with CO2 bearing gas streams, an irreversible carbonate-forming reaction followed by reversible bicarbonate forming reaction take place as per the following equations. This process involves the use of hydroxides of sodium, potassium and calcium.
In most industrial applications, no attempt is made to regenerate spent bicarbonate solution due to high steam requirement for this process. Carbon dioxide absorption into alkaline solution is adversely affected by slow conversion of dissolved CO2 molecules into more reactive ionic species. Mixing of liquid during absorption helps to achieve diffusion of gas molecules in the liquid and prolongs their contact time which adds to the former’s absorptivity.
Normality of caustic solution also affects the rate of absorptivity. With sodium hydroxide solution (NaOH), for instance, it was found that the rate of reaction is more rapid if normality lies between 2.5 to 3. Potassium hydroxide (KOH) is more commonly used in industrial scrubbing but it suffers from the limitation that it is not readily available in rural areas where biogas plants are normally located.
Calcium hydroxide [Ca(OH)2] on the other hand is generally preferred for biogas scrubbing as this chemical is more readily available and cost of operating a lime-water scrubber is also relatively less. The main limitation of lime-water scrubbing are difficulties faced in controlling solution strength, and removal of large amounts of precipitate from mixing tank and scrubber.
In most cases, sediment and suspended particulate matter need be removed in order to avoid clogging in pumps, high-pressure spray nozzles, packing and bubbling apparatus. Sodium hydroxide has the major advantage of being available in easily handled pellet forms that enable rapid and simple recharging of the scrubber. However, with NaOH solutions problems of suspended particulate matter are not totally eliminated.
The absorption of CO2 in alkaline solution is assisted by
agitation. The turbulence in the liquid aids to the diffusion of the molecule in the body of
liquid and extends the contact time between the liquid and gas. Another factor governing
the rate of absorption is the concentration of the solution. The rate of absorption is most rapid
with NaOH at normalities of 2.5-3.0.
CARBON DIOXIDE REMOVAL USING AMMONIA IN BIOGAS
Ammonia is used as an absorbent in chemical scrubbing to remove CO2 from biogas. A continuous system consisting of the 1L digester was used for biogas production which was bubbled through an absorbent in 500mL gas washing bottle at a constant temperature in a water bath. The obtained biomethane potential was found to be 0.387 m3 CH4/ kg VS which simply means that more methane gas can be obtained when using ammonia for absorption. An increase in the gas flow rate leads to an increase in the mass transfer coefficient resulting in an increase in the rate of absorption. The initial CO2 concentration affects the removal efficiency because more work needs to be done for biogas with a high initial concentration of CO2. NH3 has better absorption capacity because higher biogas purity was achieved at lower NH3 concentration. The removal efficiency for NH3 increased from 69%-79% on average with CH4 concentration reaching over 85% vol. This is equivalent to a calorific value ranging from 25- 33.5 MJ/Nm3 which is promising in terms of the gas ability to run in an automobile engine.
CARBON DIOXIDE REMOVAL USING AMMONIA IN BIOGAS
Ammonia is used as an absorbent in chemical scrubbing to remove CO2 from biogas. A continuous system consisting of the 1L digester was used for biogas production which was bubbled through an absorbent in 500mL gas washing bottle at a constant temperature in a water bath. The obtained biomethane potential was found to be 0.387 m3 CH4/ kg VS which simply means that more methane gas can be obtained when using ammonia for absorption. An increase in the gas flow rate leads to an increase in the mass transfer coefficient resulting in an increase in the rate of absorption. The initial CO2 concentration affects the removal efficiency because more work needs to be done for biogas with a high initial concentration of CO2. NH3 has better absorption capacity because higher biogas purity was achieved at lower NH3 concentration. The removal efficiency for NH3 increased from 69%-79% on average with CH4 concentration reaching over 85% vol. This is equivalent to a calorific value ranging from 25- 33.5 MJ/Nm3 which is promising in terms of the gas ability to run in an automobile engine.
Method # 3. Method Developed by the IARI, New Delhi:
T.D. Biswas, et al., developed another method for CO2 scrubbing. It was found that biogas can be removed by bubbling it through 10 per cent aqueous solution of mono-ethanolamine (MEA). By single bubbling through a plain column of 6 cm height, carbon dioxide content in biogas was reduced to 0.5-1 per cent by volume from the initial value of 40 per cent.
Scrubbing column was made of an inexpensive plastic bubbler of 5 cm diameter and 15 cm height with only one orifice. The maximum removal of carbon dioxide was observed when bubbles moved out individually without colliding one another to form a continuous stream. Optimum gas flow rate to the regulator was estimated as 100 ml per minute which gave 60 ml of purified gas per minute in the reservoir.
The decrease in this rate of flow was not found to cause any further scrubbing. The initial pressure of the gas introduced into the bubbler was 10 cm of the water column and drop in pressure head was about 5 cm of the water column. Both caustic potash and monoethanolamine solution were effective in reducing the carbon dioxide content to 0.5 to 1 per cent.
Whereas spent caustic potash solution cannot be regenerated, MEA solution can be completely regenerated by boiling for five minutes and thus can be used again and again. Furthermore, MEA solution is far less caustic than other solutions used and therefore pose much fewer hazards for the skin. This method is thus very practical and economic for biogas scrubbing.
Method # 4. Pressure Separation:
This method works on the principle of compressing biogas beyond the limit of the critical partial pressure of impurities (CO2) with a temperature greater than the critical temperature of methane but below those of impurities. For instance, carbon dioxide liquefies when the gas temperature falls below 89.6 F (32 C) after compressing beyond 1106 psi (77.76 kg/cm).
Thanks, http://www.geographynotes.com/
Pressure Swing Adsorption (PSA) Systems for CO2 and Hydrogen Sulphide Scrubbing
Pressure swing adsorption (PSA) systems, can be thought of as being molecular-sieves for carbon. PSA has been described are the second most commonly used biogas upgrading technology in Europe, after water scrubbing which is most likely the most popular. A typical system is composed of four vessels in series that are filled with adsorbent media which is capable of removing not only the CO2 but also water vapour, N2, and O2 from the biogas flow.
Typically in order to eliminate CO2 from biogas, the PSA upgrading takes place over 4 phases: pressure build-up, adsorption, depressurization and regeneration. The pressure build-up occurs by equilibrating pressure with a vessel that is at depressurization stage. Final pressure build-up occurs by injecting raw biogas. During adsorption, CO2, N2, and O2 are adsorbed by the media and the purified gas discharges as pure methane to a quality which will be far less corrosive and has a higher calorific value.
Recently developed gas-liquid membranes have been introduced, which operate at atmospheric pressures thereby reducing the energy consumption of compression. The use of specific solvent solutions allows the separation and recovery of the H2S and CO2.
Another approach to improving the economics of gas upgrading has been to recover the CO2 by cooling and recovering dry ice. This can then be sold as an industrial gas whilst the biogas is either used in its more concentrated form (80-90% CH4) or further refined to vehicle quality standard (>96% CH4).
Pressure Swing Adsorption
Pressure swing adsorption (PSA) is a method for the separation of carbon dioxide from methane by adsorption/desorption of carbon dioxide on zeolites or activated carbon at alternating pressure levels. This technology is often applied in the gas treatment industry as it also effectively removes volatile organic compounds, nitrogen and oxygen from industrial gas streams.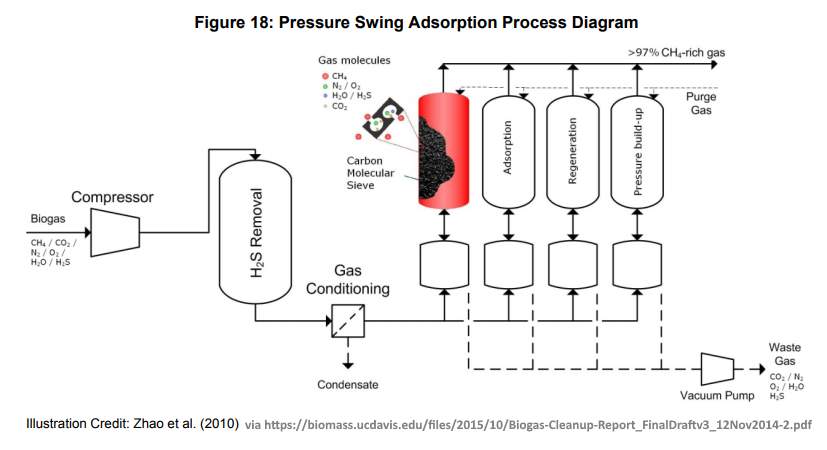
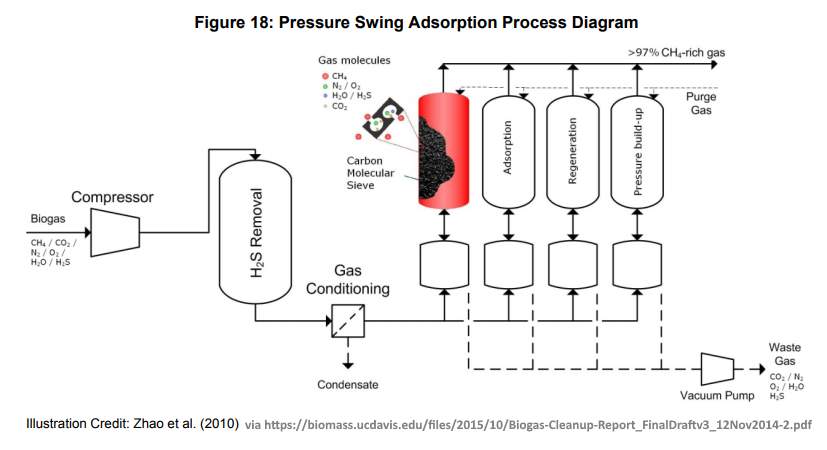
This comment has been removed by a blog administrator.
ReplyDelete